
APPROFONDIMENTO ISPEZIONE RACK Analisi criticità - Metodo e procedura di verifica.

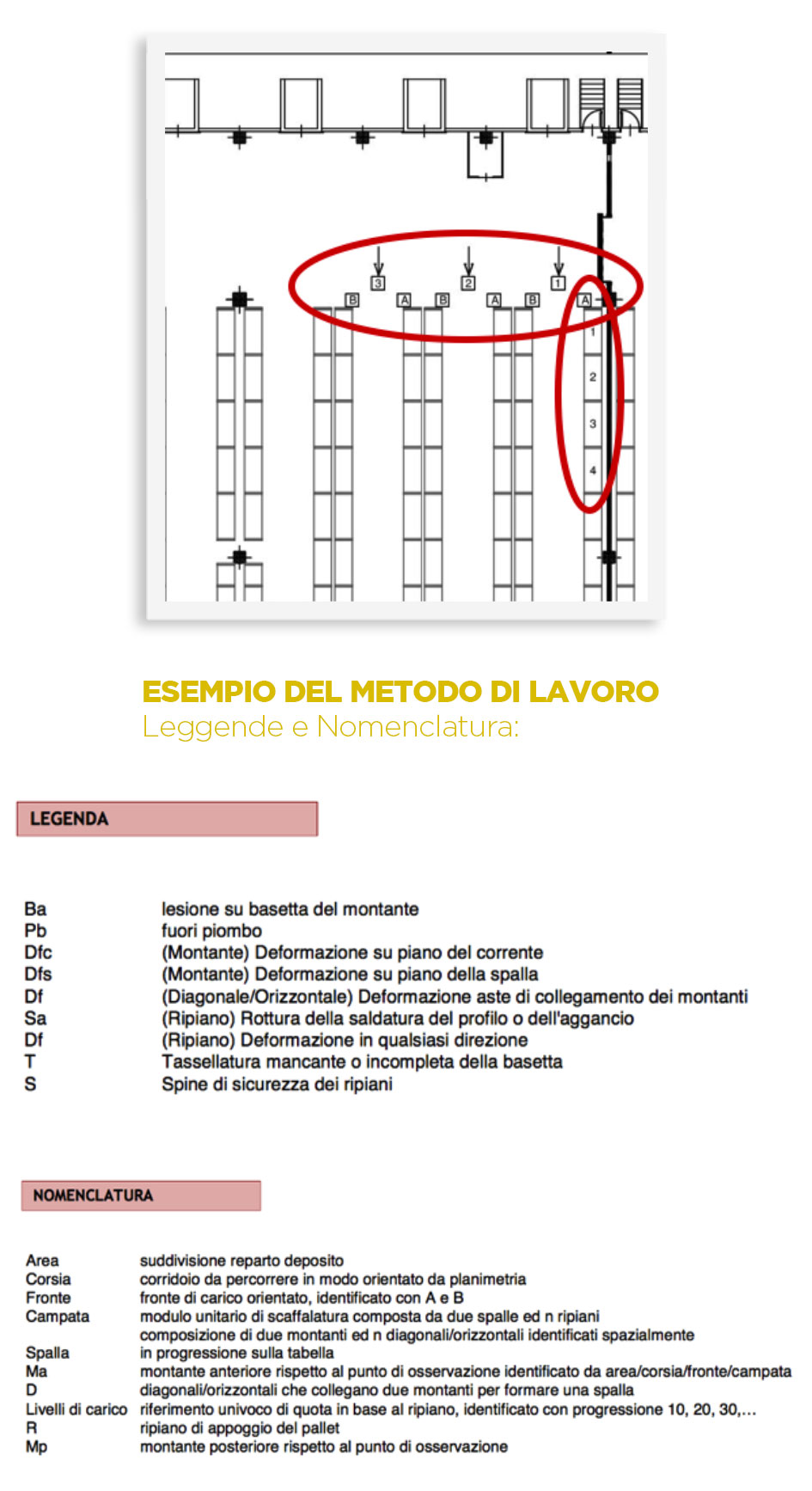
Finalità: Verifica ispettiva periodica finalizzata al monitoraggio per la prevenzione dei danni e degli incidenti derivanti dall'operatività delle aree stoccaggio negli ipermercati e nei depositi.
PREMESSA
L'attività di verifica esclude tutte le scaffalature leggere, le gondole espositive ed ogni altro arredo mobile espositivo.
In questa fase vengono prese in considerazione le scaffalature di stoccaggio rientranti fra le installazioni fisse e, fra queste, la tipologia destinata allo stoccaggio di pallet.
Successive integrazioni possono riguardare sia particolari configurazioni della tipologia presa in considerazione, tipo le postazioni picking, caratterizzate dalla presenza di ripiani a ridotta distanza e coperti da coppelle in lamiera, oppure dotazioni speciali, tipo le rulliere.
RIFERIMENTI NORMATIVI
Vengono prese in considerazione le produzioni manualistiche di vari produttori, le principali norme generali di sicurezza aggiornate al momento dell’incarico, con particolare riferimento al D.Lgs. 81/08 e s.m.i., oltre alle norme tecniche applicabili, in particolare la norma europea UNI EN 15635 “Sistemi di stoccaggio statico – Utilizzo e manutenzione dell'attrezzatura di immagazzinaggio”. Tenendo un occhio particolarmente attento alle problematiche statiche sismiche, da valutare attentamente in funzione anche delle aree in cui si insiste.
METODO DI LAVORO:
- Fase 1. Identificazione spaziale delle scaffalature. La metodologia proposta raccoglie parte delle esperienze e della cultura della gestione operativa dei depositi e della logistica di magazzinaggio in generale per la gestione delle posizioni. Trattandosi di interventi sulle scaffalature nel loro complesso occorre integrare la logica del “posto-pallet” con riferimenti idonei atti ad identificare tutta la componentistica. L'identificazione avviene pertanto con una sequenza coordinata così suddivisa: Area: suddivisione di reparto del deposito/riserva (es. scatolame, bevande,...). Corsia: corridoio da percorrere in modo orientato secondo planimetria, identificato da numero (es 1, 2, 3,...); nella planimetria la posizione della numerazione ed una freccia indicatrice del percorso identificano la direzione. Fronte: prospetto della scaffalatura come si affaccia sulla corsia, identificato con lettera, numero,... (es. A sinistro, B destro) Campata: modulo unitario di scaffalatura composto da due spalle ed n ripiani, identificato con numero progressivo dal punto di inizio di ciascuna corsia (1, 2, 3,...). Spalla: composizione di due montanti ed n diagonali/orizzontali resi solidali mediante bullonatura o saldatura per formare l'elemento strutturale verticale Montante: parte verticale portante della spalla; ogni montante si può identificare spazialmente come anteriore e posteriore rispetto al fronte. Diagonale: asta di collegamento e distanziamento fra i montanti, non sopporta carichi di flessione; alla base ed in sommità della spalla l'asta è orizzontale. Livelli di carico: sono i ripiani sui quali è collocata la merce su pallet; secondo una delle consuetudini di numerazione in questo contesto ogni livello è identificato da una decina (10, 20, 30,...); il livello è utile per indicare con buona approssimazione anche la posizione dei danni alle spalle. Un esempio di identificazione può essere: A-1A-12-30: identificherà Area (A), Corsia (1), Fronte sinistro (A), Campata (12), Terzo ripiano (30)
- Fase 2. Analisi dei danni. La verifica interessa le tipologie di danno da utilizzo che si possono riscontrare a carico dei vari componenti. I valori di misura e le tolleranze ammissibili rispondono ai criteri della norma UNI EN 15635 e sono esplicitati nella relazione tecnica. La tabella di verifica predisposta consente una compilazione progressiva che accompagna il tecnico verificatore affinché sia agevole identificare i vari componenti e vi sia continuità tra osservazione e compilazione. Sono state identificate e raggruppate le tipologie di rischio e ad esse viene assegnato un punteggio in base alla gravità del riscontro: - nessun riscontro → situazione regolare; - valore 1 – danno lieve → la situazione è segnalata ma l'utilizzo può continuare in sicurezza; nella tabella appare un indicatore verde; - valore 2 – danno medio → la situazione richiede una limitazione di esercizio (p es. non ricaricare un ripiano dopo il prelievo della merce presente e provvedere ad un intervento successivo); nella tabella appare un indicatore giallo; - valore 3 – danno grave → la struttura interessata deve essere immediatamente scaricata e resa inutilizzabile fino ad intervento di ripristino; nella tabella appare un indicatore rosso. I danni valutati ed i conseguenti livelli di rischio stimati sono ripartiti in: Montanti (suddivisi in anteriori e posteriori): - danni alla basetta d'appoggio; - fuori piombo globale; - deformazione in direzione del ripiano (da urto laterale); - deformazione in direzione della spalla ( da urto frontale). Diagonali/orizzontali: - deformazione in qualunque direzione. Ripiani: - deformazione in qualunque direzione; - danni/incrinature alle saldature dei traversi e/o dei connettori ad incastro. Ulteriori elementi di valutazione interessano l'assenza di componenti che devono essere ripristinati per l'operatività in sicurezza. Sono considerati i seguenti componenti: - tassellatura della basetta dei montanti; - presenza delle spine anti-sfilamento dei ripiani; - assenza critica di ripiani che può determinare instabilità del montante; - assenza o danneggiamento della protezione antiurto fissata a terra. Periodicità del monitoraggio. Secondo UNI EN 15635 l'intervallo tra due verifiche non deve superare i 12 mesi.
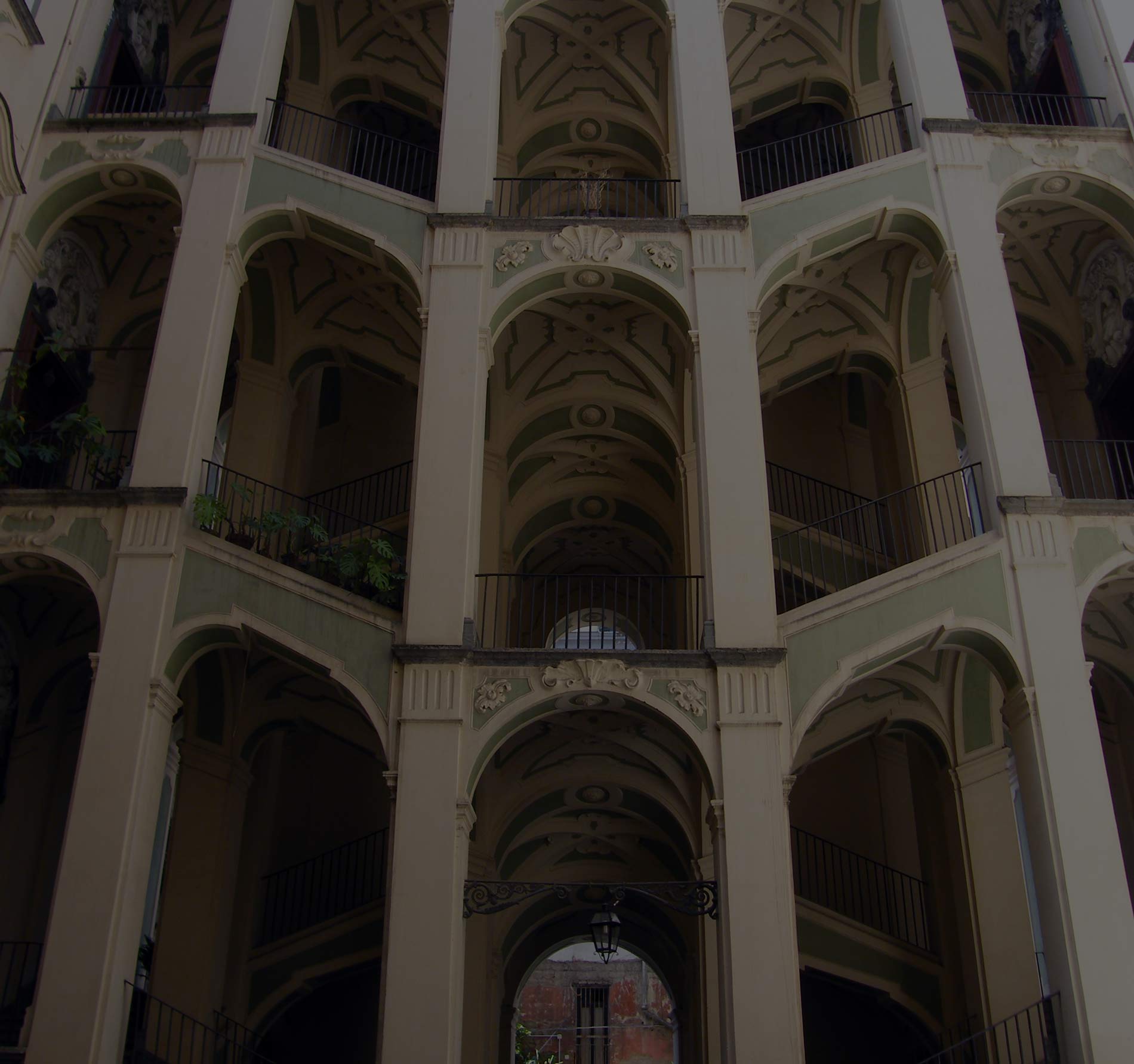